Polyurethanes
that fit YOUR process.

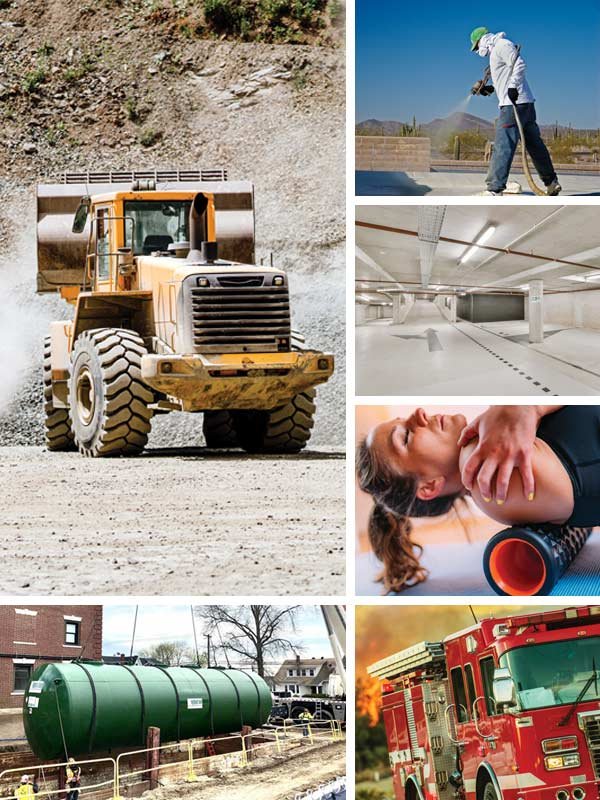
Providing Polyurethanes Since 1997
At Chemline, we engage in a co-creation process with end users and ensure our products are perfectly tailored to meet their specific needs in terms of fit and functionality. To support this approach, we maintain three analytical laboratories operated by a team of over a dozen skilled chemists and technicians, enabling us to offer rapid turnaround times. Our technical partnerships with global polyurethane suppliers ensure we consistently have access to the highest-quality raw materials available.
Proudly Manufactured in the USA
- Large investment in batching equipment with capabilities of processing anywhere from 5 to 4,400-gallon batches to ensure flexibility and a high degree of customization in manufacturing
- Automation in equipment, processes and training of personnel to ensure a consistent product
- Extensive raw material storage that protects customers from supply interruptions
- ISO 9001:2015 certified
- Processing capabilities for low NCO to Quasi prepolymers
- The shortest lead-times in the industry with 99% on-time deliveries
Graco Systems Support and Expertise
Our Technical Services Team is equipped with a wealth of field experience and a broad range of application expertise. Their primary role is to offer exceptional on-site technical support to our customer base across North America.
The team specializes in guiding users in the effective use and maintenance of Graco spray equipment, providing repair services, conducting training sessions, troubleshooting issues, and delivering on-site application assistance.
Our active and consistent engagement ensures each of our customers benefits from tailored, expert support, directly addressing their specific needs, increasing throughput minimizing waist and unnecessary expense.
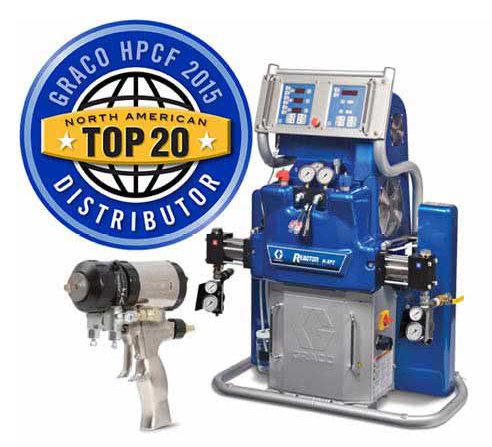

Chemline’s Polyurea secondary containment is ideal for preventing leaks and containing spills of...
Cold cast polyurethane elastomers and foams are used in a wide variety of applications...
Hot Cast urethane prepolymers are used in the most rigorous applications where the...
Polyurethane flexible foam systems can be specially formulated to feature reduced...
Chemline's Geotechnical foam was specially formulated for slab lifting and soil...

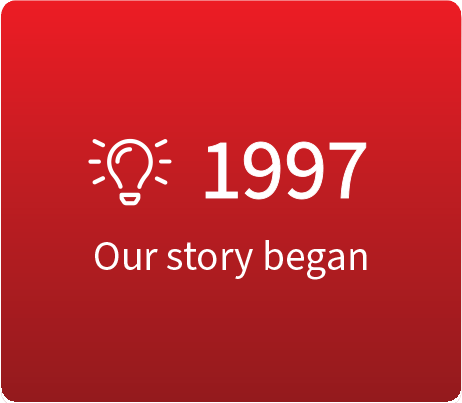
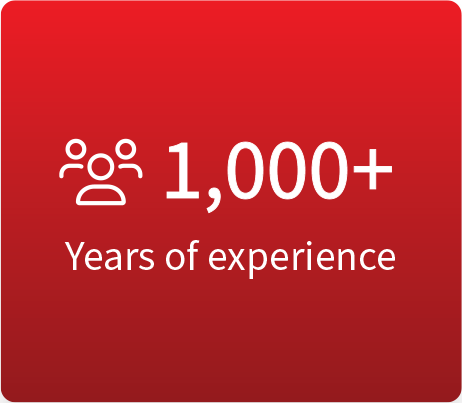
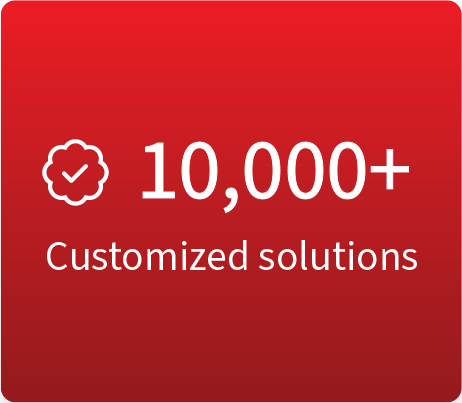
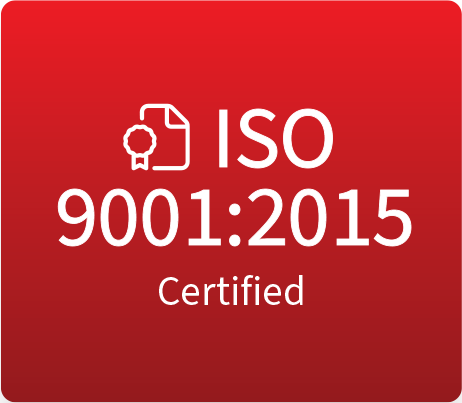
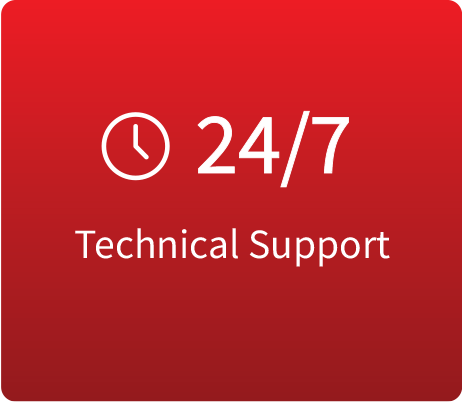
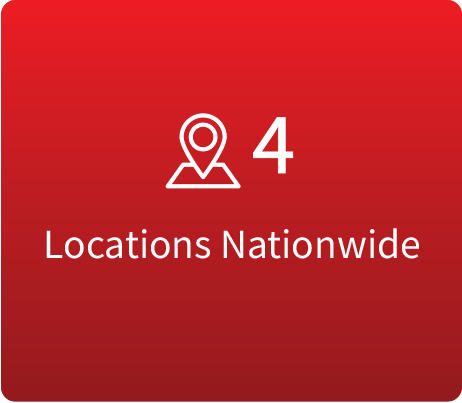

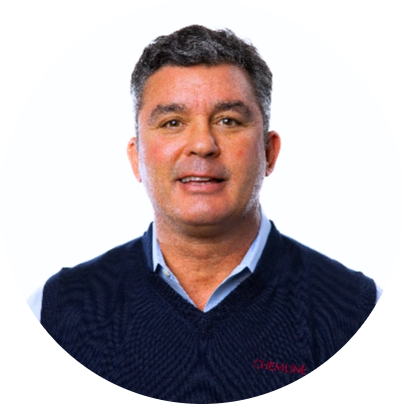
"
No one will out-formulate us, no one will produce quality product faster, and no one will cradle and serve the customer like Chemline!"
- John Pantanella, CEO and Founder